Optimisation of Adobe Production at Ghadames, Libya
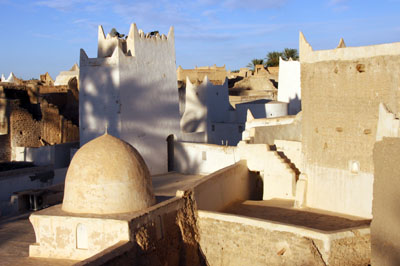

Satprem Maïni, Director of the Auroville Earth Institute was invited in November 2008 by CRATerre-ENSAG to improve, restructure and optimise the mass production of adobes for the restoration of the centuries-old town of Ghadames in Libya.
Ghadames has been declared by UNESCO as a World Heritage Site. Ghadames is an oasis in the desert very close from the borders of Algeria and Tunisia, at around 700 km southwest of Tripoli. It lies in beautiful landscapes of rocky desert and sand dunes. The architecture and urban pattern of Ghadames has been adapted over the ages to the extreme Saharan climate. The old town had a population of about 7000 people at a time with about 1600 multi storey houses. Around 1982, people were moved into modern houses which were built by the government, south side of the old town and the latter was abandoned.
Ghadames is presently restored in the overall framework of the cooperation programme between Ghadames City Promotion and Development Authority (GCPDA), Engineering Consultancy Office for Utilities (ECOU) and the International centre for earth construction-High School of Architecture of Grenoble, France (CRATerre-ENSAG). About 100,000 adobes have to be moulded for restoring the old town.
The aims of the mission of Satprem Maïni which was conducted from the 1st to 26th November were:
• Identification and selection of soils
• Trials on various mixes for the production of raw adobes
• Trials on stabilisation of adobes with local stabilisers
• Improvement and optimisation on the use of mixers
• Quality control and optimisation on the production of adobes
• Optimisation of the transportation and life cycle of the adobes from the brickyard to the site
The soils in Ghadames are relatively difficult. First because they are all salty as an ancient sea was in this area very long ago and second because the soils are very silty with in general a lot of variations depending on the depth of the veins and the location in the quarry.
11 soils from 7 different locations were identified and evaluated. Various quarries or possibility of sources for soils were inspected and sensitive analyses were conducted. Five test pits were totally dug with a bulldozer in a quarry so as to identify the nature and depth of layers. The selected veins and soil types were then mixed by the bulldozer.
24 different mixes were done with 10 different soils from 6 various locations. The mixes were done either by hand or with a mixer.
18 different mixes were done with 4 different soils from 4 various locations and 4 stabilisers (Industrial lime, local grey gypsum, industrial gypsum from Tripoli and cement resistant to salt). Percentage of stabilisers was kept around 6.6%. The main aim of the stabilisation was to evaluate the effectiveness of these stabilisers on different soils so as to increase their water resistance.
Two tests were elaborated to evaluate the adobes qualities with very simple means:
• “Water drip” test conducted on raw adobes: 1.5 litres of water was poured through a ø 5 mm hole at the height of a water bottle. This test was meant to test cohesiveness and the resistance to the impact of storm rainwater and to the water runoff, as the tested adobe was sloping down. The depth of penetration was measured.
• Absorption test conducted on stabilised adobes: 1 litre of water was poured on an adobe which was surrounded by a border of clay. The area in direct contact with water was about 700 cm2. The absorption time was measured, the resistance to penetration was evaluated with a finger print and the depth measured.
Some tools were manufactured so as to have a higher productivity and a better quality of the adobes. The organisation of the new production line was based on mechanising the production, especially for the preparation of soils and the mix, from crushing, sieving to mixing:
• Crushing lumps of clay with the back of the bucket of the dumpy loader.
• Sieving with a dumpy loader directly on the large metal sieve especially manufactured for that. This method allowed to sieve about 4-5 m3 per hour.
• Mixing with a motorised mixer which was loaded by wheelbarrows climbing on a ramp. This method allowed delivering enough mix to 7 adobes moulders.
The new production of adobes started just 2 days before the end of the mission, on the 23rd and 24th November but the procedure set up allowed the local team to produce now in December 3000 adobes per day.
Many people helped for the success of this mission and we want to thank especially:
Mr. Boukhari Hoda, Director, Secretary of the executive committee of GCPDA
Mr. Nuri Aweti, Architect, advisor, ECOU
Mr. Ibrahim Bachir Malik, Head of Ghadames Old Town Administration Office (GOTAO)
Mr. Mohammed Boukhari, Contractor of Ghadames
Mr. Thierry Joffroy, President of CRATerre
Mr. Grégoire Paccoud, permanent staff of CRATerre in Ghadames
All workers who worked hard for the trials and who are now producing the adobes
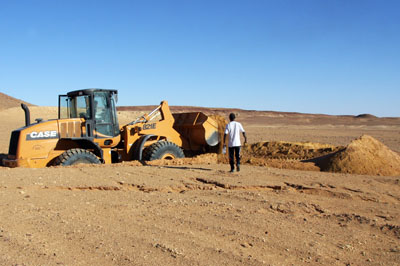
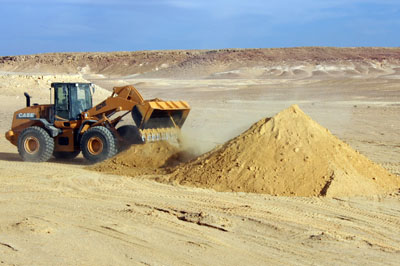
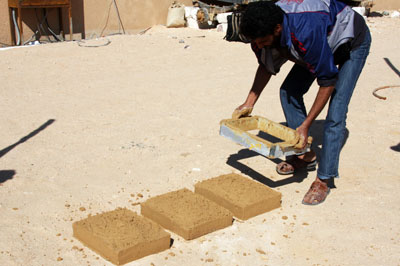
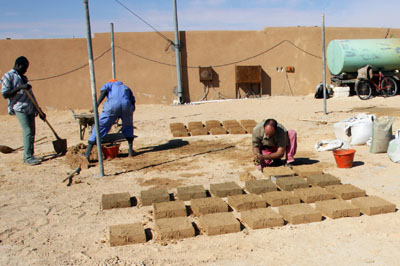
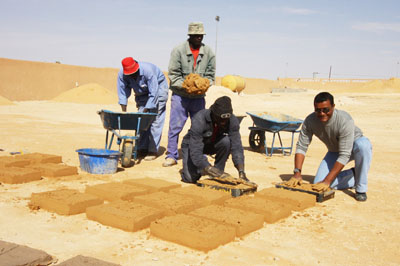
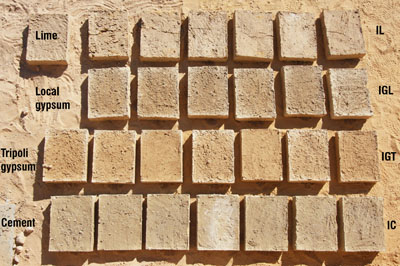
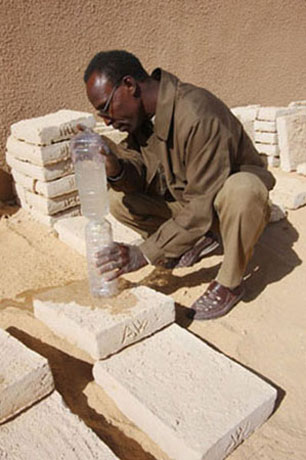
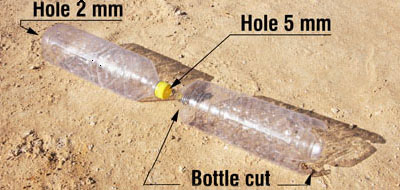
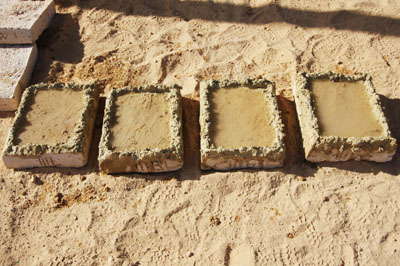
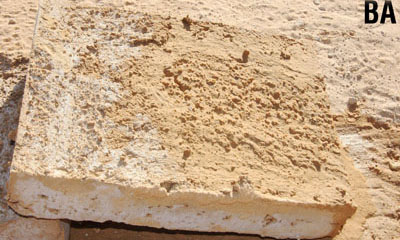
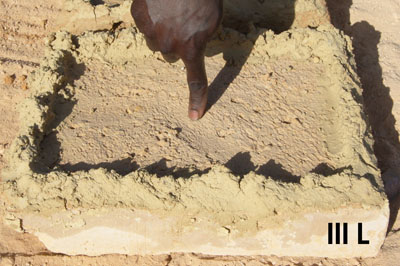
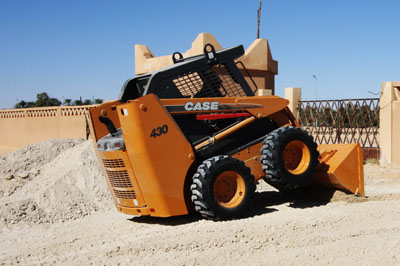
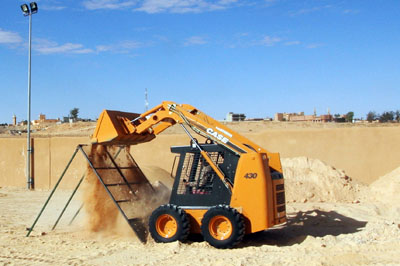
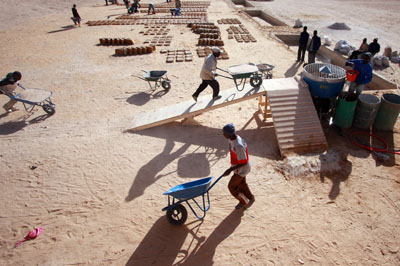
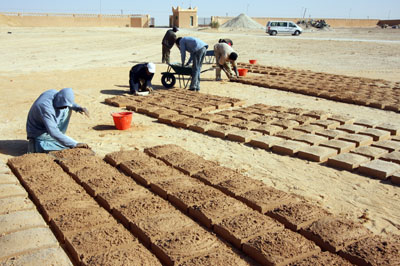
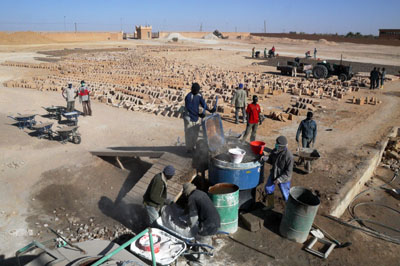
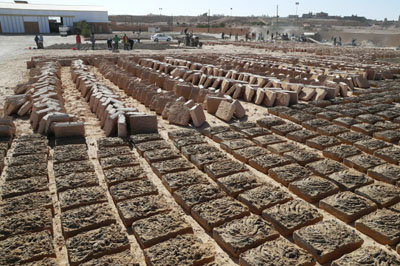

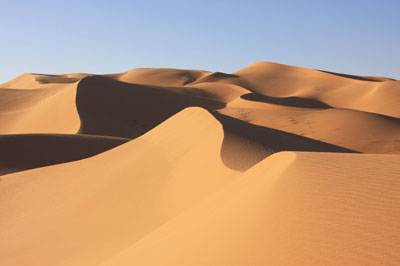
Contact US
- Address:Auroville Earth Institute, Auroshilpam, Auroville 605 101 - T.N. India
- Phone:+91 (0) 413 - 262 3330 / 262 3064
- Email:info@earth-auroville.comOpens in your application